Auto Build Assembly Item
Access to this feature may only be available
with the ‘Complete’ edition. Ask your Wasp representative for details.
TThe Auto Build feature as the name indicates eliminates most of the
steps generally required for a Build
Assembly Item to streamline the process. Since most of the steps have
been removed, there are limitations to which Assembly
Items can be automatically built. Most of the limitations are related
to the sub items that make up the Bill of Materials. The limitations are
as follows:
- The items in the Bill of Materials should be
located only in one location that the user has access to, or have
only one primary location in the currently selected working sites.
- The items in the Bill of Materials should not
have any required trackby fields.
The reason for these limitations is because the AutoBuild process will
automatically select and remove the Bill of Materials for the Assembly
item, but it can only do so if there is no ambiguity in the inventory
needed to be removed.
Keep in mind that while you can add Assembly Items through the Adjust and Audit
functions, doing this will not affect
the inventory amounts for the sub items. You should only add Assembly
Items using these functions if you want to add inventory to an Assembly
Item due to a return or Audit discrepancy. To increase your inventory
for an Assembly Item and decrease your inventory for the sub-items, use
the Build or AutoBuild feature.
To Auto Build Items:
- Click on the
Products > Build.
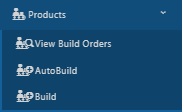
- The Auto Build screen will appear.
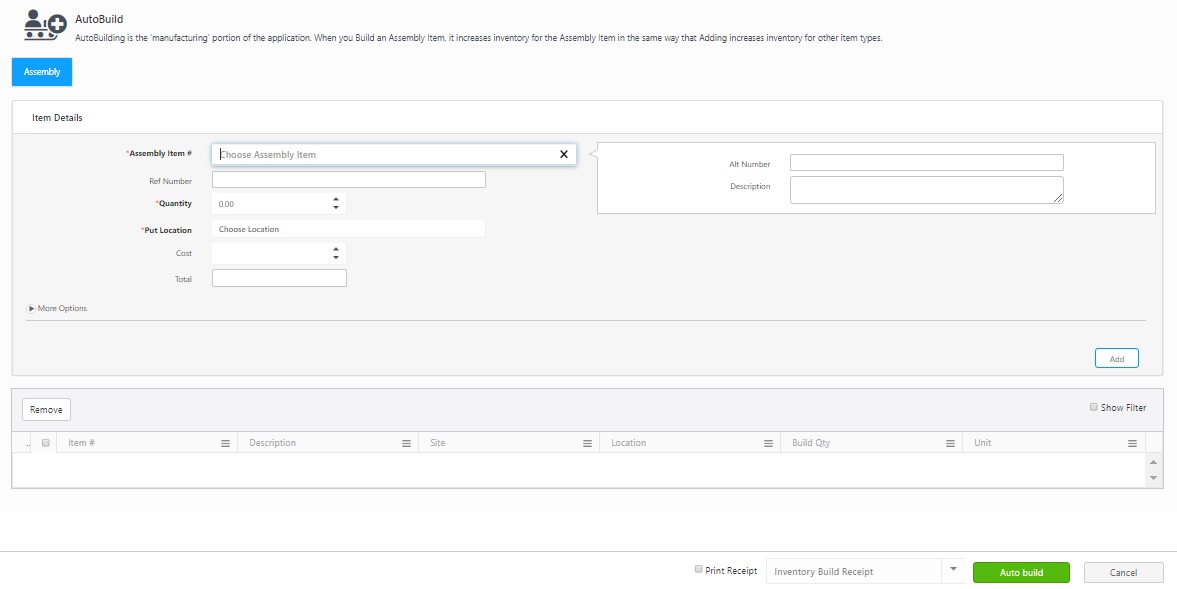
- Assembly
- Assembly Item # - Choose/Enter the Assembly
Item you want to autobuild.
- The Alt Number
and Description will populate
based on the Assembly Item you select.
- Reference Number - Enter the reference number.
- Quantity - Enter the quantity you want to build.
- The Cost
is automatically calculated based on information entered for the components. This
Cost reflects the cost of the entire Assembly Item (including sub-items).
Cost is per build and is a required field. The Total
Cost is the total cost based on the quantity being built.
- Put Location - Enter a Put Location for
this Assembly Item. If a primary location was set for this Assembly
Item on the New/Edit Assembly Item screen, the location will automatically
appear here. You can change this location as needed.
- If you setup any Track
By fields when you created this Assembly
Item, the Track By
section will be enabled. These Track
By fieldsIf this item has track bys set, a button labeled Tracking Details will appear: Refer
Tracking Details.
- Click on the More Options. Enter Notes,
if any.
- Click on the Add
button to add this Build to the list at the bottom of
the screen.
- To update the added Item details, click
on the item in the bottom grid. The Item Details will get populated.
Make the changes and click on the Update
button.
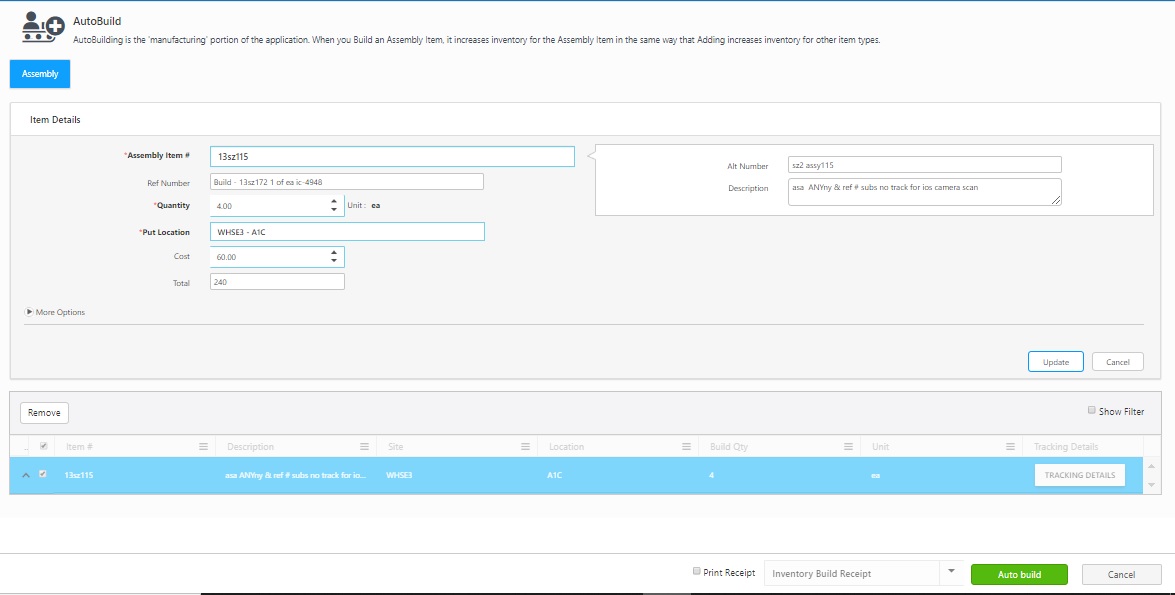
- Print Receipt
Checkbox - Click on the checkbox to print a receipt. If you
want to change the receipt header name, enter the name in the text
box next to the checkbox. Note:
In case the pop-ups are blocked and you are unable to view the print
receipt, Refer Popups
and Redirects to allow pop-ups and to view the print receipt.
- Click on the Auto
build button.